Écoutez cet article
A l'achat de notre vedette Amerglass, nous savions que l'installation électrique était à reprendre dans sa globalité. Pour la partie gestion des consommateurs, comme les éclairages, les frigos ou les pompes…, nous avons opté pour un "tableau intelligent", en nous appuyant sur la technologie EmpirBus. Mais en amont de cette installation, il fallait encore connecter les différents éléments : batteries, alternateurs, chargeur, panneau solaire, régulateur…
Estimer les besoins
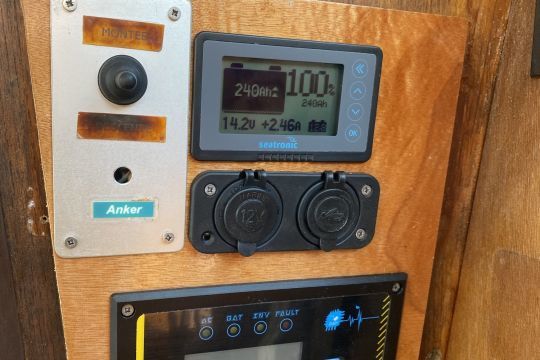
Sur le plan des besoins électriques, nous avons besoin d'une certaine autonomie au mouillage, pour éviter d'avoir à démarrer les moteurs pour recharger les batteries. Nous avons souhaité avoir sous les yeux un gestionnaire de batterie qui nous informe de l'état de notre parc. Enfin, il nous a paru souhaitable d'installer un convertisseur 12-230 V, pour utiliser certains équipement en 230 V même quand nous ne sommes pas branchés au quai. Bien entendu nous avons complété l'installation par un chargeur, utilisé quand nous sommes au port branché sur la prise 230 V.
3 batteries : deux servitudes, une démarrage
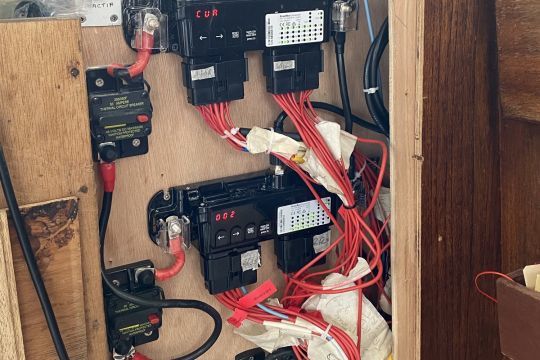
Lors de notre achat, l'Amerglass était équipée de 3 batteries qui avait été remplacées l'année précédente. Trois batteries au plomb identiques de 120 Ah chacune. Nous avons donc décidé de les conserver, en en dédiant une comme batterie de démarrage pour les 2 moteurs, et les 2 autres faisant office de batteries de servitude.
Un chargeur 3 en 1
A partir de ces postulats, aidés par Seatronic, nous avons dessiné le schéma électrique du bateau.
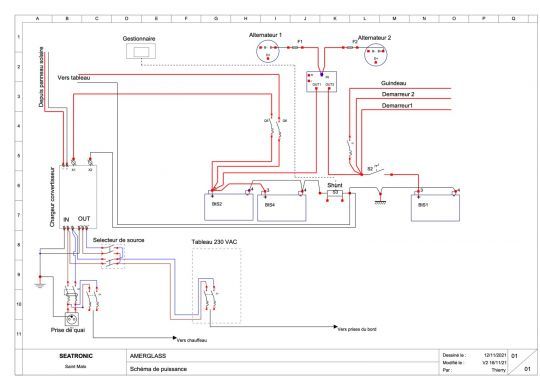
Celui-ci nous a conseillé l'installation d'un produit 3 en 1 nouvellement importé. Il s'agit d'un chargeur - convertisseur - régulateur de panneau solaire. Ce produit recharge les batteries quand il est alimenté en 230 V, converti le 12 V en 230 V avec une puissance 1000 W, et intègre un régulateur MPPT pour gérer des panneaux solaires, dans notre cas, 2 fois 110 Ampères en rigide disposés sur le rouf. Cet appareil dispose aussi d'un panneau de contrôle déporté. Nous avons donc installé ce chargeur 3 en 1 dans la cale moteur, proche des batteries, et le panneau de contrôle près du poste de barre.
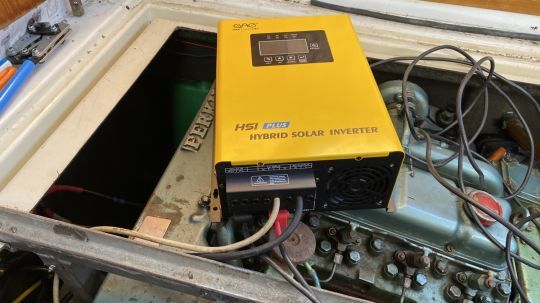
C'est aussi Seatronic qui nous a fourni le gestionnaire de batterie. Un modèle de sa fabrication simple à interpréter et très fiable.
Un circuit 230 V toujours disponible
Pour obtenir du 230 V toujours disponible à bord, la machine à glaçons fonctionne en 230 V…, nous avons été obligés de passer par un sélecteur de source. C'est un coupe-circuit qui connecte le 230 V issu du quai, ou bien celui venant du convertisseur. Une position neutre coupe les 2 circuits.
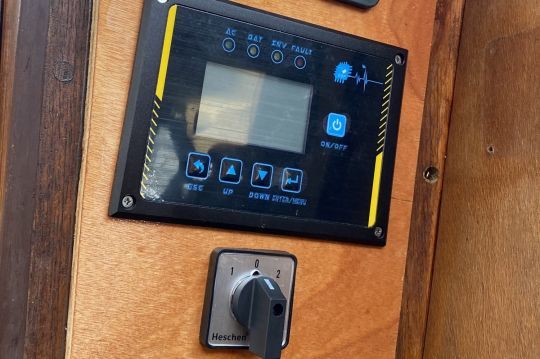
Des protections obligatoires pour le circuit 230 V
Les différentes prises 230 V du bord sont protégées par un disjoncteur 10 Ampères. Mais en amont, juste après la prise de quai, nous avons installé un disjoncteur différentiel, qui évite tout risque d'électrocution. Ces différents disjoncteurs sont du matériel que l'on retrouve dans nos habitations terriennes. Ils sont juste installés dans un boitier dont la porte est étanche, IPX4.
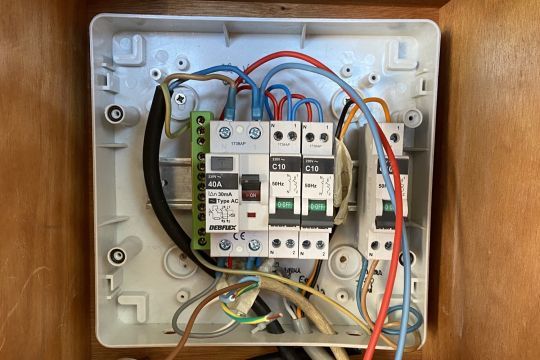
Disjoncteur de protection 12V
Pour les protections de tous les éléments du circuit 12 V, comme les batteries ou le guindeau, nous avons utilisé du matériel Blue Sea. Que ce soit des porte-fusibles ou des coupe-circuits, il s'agit de matériel de qualité marine reconnus pour leur sérieux.
Ainsi, le chargeur de batterie est protégé par un disjoncteur 50 Ampères. Tout comme les 2 Connect50 EmpirBus. Idem pour les panneaux solaires qui sont protégés par un disjoncteur 50 Ampères. Ces protection peuvent se disjoncter manuellement pour déconnecter du circuit l'un ou l'autre équipement, en cas de problème ou simplement pour l'entretien.

Pour le guindeau, nous avons choisi un disjoncteur de 80 Ampères, défini ainsi en fonction des caractéristiques de notre guindeau électrique. Enfin, un coupe-circuit général bipolaire isole la batterie moteur.
Le parc servitude est protégé par un fusible 300 Ampères installé juste à côté des batteries, afin d'éviter tout risque d'incendie à bord.
Pour la charge des batteries, les 2 alternateurs des deux moteurs, se rejoignent pour entrer dans un répartiteur de charge sans perte. Ce boitier recharge en priorité la batterie moteur, avant de basculer sur le parc servitude.
Des cosses étanches partout
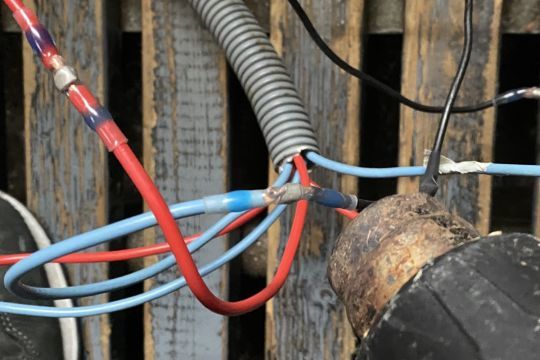
La réalisation de tout ce circuit électrique s'est fait simplement en suivant le schéma, et en reliant les différents câbles entre eux. Toutes les connexions ont été réalisées avec des cosses serties et étanchées avec de la gaine thermoretractable. Soit de la gaine uniquement pour les grosse cosses, soit des cosses thermorétractables elle-même. Nous avons fait ce choix pour éviter l'étamage. En effet, étamer un fil le protège de l'oxydation mais il devient cassant, c'est pourquoi dans l'aviation, on n'utilise plus cette méthode. La solution des cosses étanches est alors préconisée.
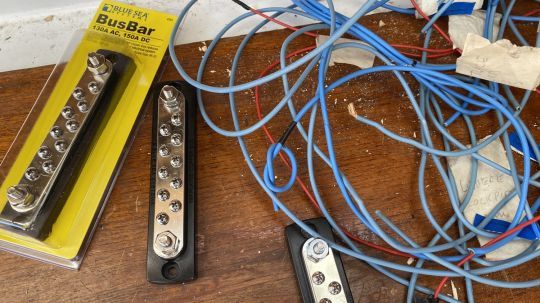
Certes, le budget d'une cosse étanche n'est pas le même que celui d'un fil étamé, mais il assure un bon contact pérenne, même dans des conditions d'utilisation sévères.
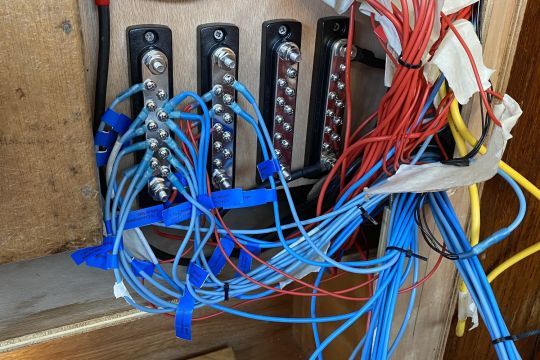