Nous sommes en 1995. À cette époque, il y a plus de 25 ans, les premiers voiliers construits en infusion étaient les J/110, un procédé de fabrication sous une licence appelée "Scrimp Process" qui depuis est tombé dans le domaine public. Historiquement, J Composites a été le premier chantier en Europe à construire un voilier en infusion. Cela illustre bien l'avance et l'expertise prises par le chantier dans ce procédé.
L'expertise de cette technique de construction permet une parfaite maîtrise de tous les aspects de l'infusion. Aujourd'hui, les pièces structurelles qui composent un J Composites (coque, pont, cloisons…) sont toutes réalisées en infusion.
Pour de nombreux chantiers navals qui utilisent aussi cette technique, ce choix a été imposé pour répondre à des normes européennes d'émanation du gaz styrène et respecter des conditions de travail pour les employés. Des raisons industrielles et environnementales. Chez J Composites, ce choix est avant tout un choix technique utilisé uniquement pour les caractéristiques mécaniques qu'offrent les pièces construites en infusion.
L'infusion c'est quoi ?
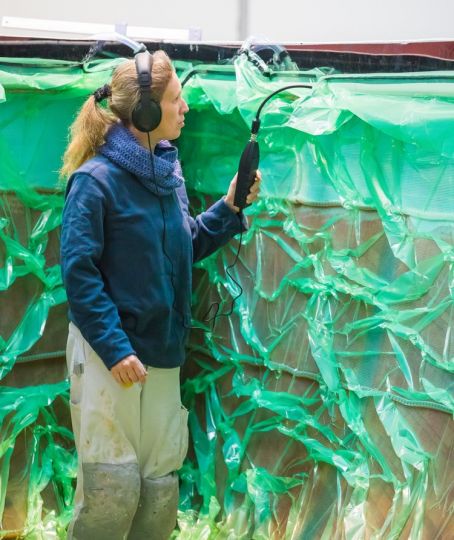
Il s'agit de disposer tous les éléments qui composent la pièce dans le moule, puis de les recouvrir avec une bâche étanche. En aspirant avec une pompe, on crée le vide qui plaque bien chacune des couches. On laisse ensuite pénétrer de la résine par des tuyaux (ligne de diffusion). Aspirée par le vide, la résine se répartit de manière équitable dans tous les tissus.
Pourquoi l'infusion ?
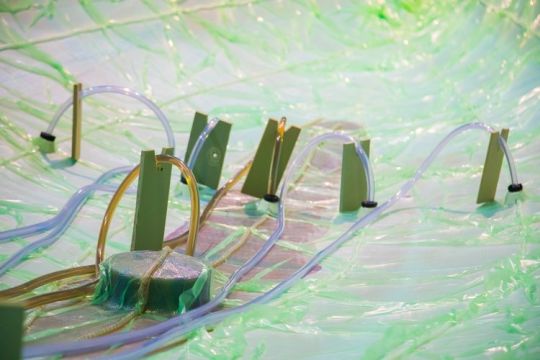
Construire en infusion permet une parfaite cohésion des pièces en compactant parfaitement les tissus entre eux. En plus, on est certain d'obtenir une bonne imprégnation de résine de tous les tissus. Et surtout, on contrôle parfaitement le poids de la pièce finie en injectant une quantité très précise de résine, ni plus ni moins.
Quand on parle de bonne imprégnation, il est bon de préciser ce qu'est un bon % d'imprégnation. Ce propos s'illustre en comparant les différentes solutions :
- Stratifié industriel = 30% fibre + 70% résine
- Stratifié manuel soigné = 40% fibre + 60% résine
- Infusion = 60% fibre + 40% résine
Considérant que la résine sert juste de colle pour permettre à la fibre de développer ses caractéristiques mécaniques. Il en faut suffisamment, mais en mettre trop n'ajoute que du surpoids sans amélioration des caractéristiques mécaniques.
Au final la pièce infusée est plus raide et plus légère que la même pièce stratée à la main. Pour un voilier, raideur et légèreté riment avec performance…
Pourquoi du sandwich ?
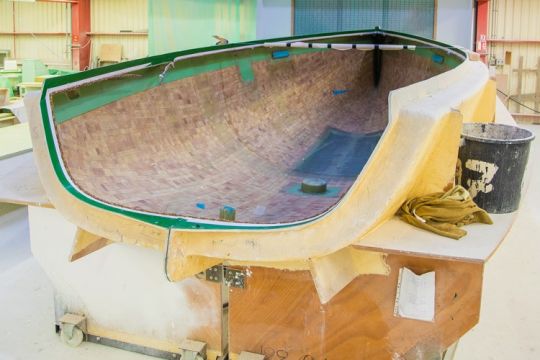
J Composite utilise du sandwich plutôt que du monolithique pour réaliser ses bateaux. En effet, une même pièce avec la même résistance pèse 1,5 à 2 fois plus lourd que la même en sandwich. En plus, une pièce en sandwich est beaucoup plus raide que son homologue en monolithique.
Quel matériaux pour l'âme du sandwich ?
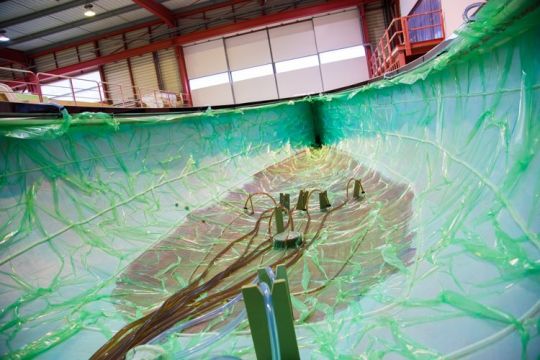
J Composites utilise 2 types d'âme : de la mousse et du bois (balsa). Le choix est principalement dicté par les formes de coque très arrondies des J Boats. En effet sur les surfaces planes, peu développées, on peut utiliser une âme en mousse. Mais sur les courbes, le balsa (notamment l'Extra Light utilisé au chantier), même s'il est un peu plus lourd que la mousse, épouse mieux les formes et limite les apports de résine. Au final, le sandwich est plus léger que s'il était totalement en mousse.
De plus, le balsa résiste mieux à la compression, aux impacts. Ainsi les fonds de coques (les œuvres vives) sur lesquels viennent heurter les vagues, sont tous réalisés avec un sandwich balsa. Les bordés, surfaces plus planes sont en mousse.
Pour ajuster l'âme dans le moule, J Composite fait appel à des préparateurs manuels. Ils ont en charge d'ajuster au plus près les différents panneaux pour éviter les interstices entre eux. En effet, ces dans ces creux que s'installe la résine. Or la résine est plus lourde que l'âme. Augmentant d'autant le poids de la coque sans la rendre plus solide pour autant. Ce travail manuel d'ajustement assure une parfaite qualité du sandwich. Une approche industrielle avec de la découpe numérique pour une pose rapide par un préparateur n'a pas autant de précision d'une pose manuelle plus longue et plus minutieuse.
Infusion comment ça marche ?
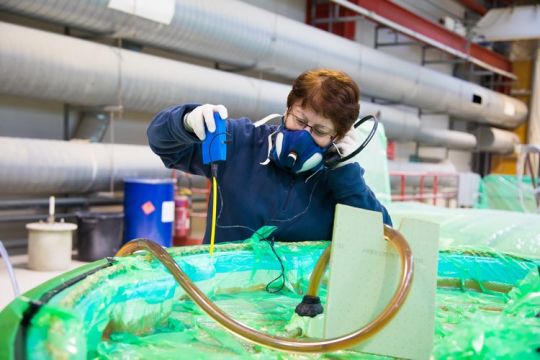
Pour être bien infusé, un strict process doit être respecté à la lettre. Une fois la coque prête, bâchée, un opérateur met en route la pompe à vide. Celle-ci crée une dépression à -1013 hPa. Il cherche alors à repérer d'éventuelles fuites d'air avec un détecteur de dépression. Il est alors encore temps de les colmater. Tout le temps que va durer l'infusion (environ 1 heure pour J 112), il va effectuer un contrôle visuel de la bonne circulation de la résine. Les lignes de diffusions (5 sur chaque bord) sont ouvertes successivement depuis le fond de coque, en remontant progressivement sur les bordés.
Il faut parfaitement maîtriser la température pendant toute cette phase. C'est elle qui assure la fluidité et la prise de la résine. En effet, s'il fait trop chaud, la résine sera trop fluide et catalysera trop vite, alors que s'il fait trop froid, la résine trop épaisse ne se diffuse pas bien.
Après cette heure d'infusion, la pompe à vide continue de tourner pour assurer le vide et bien compacter les tissus pendant tout le temps de séchage de la résine. C'est aussi un gage de qualité de construction.