Au cœur de la Forêt-Noire, loin des embruns salés, Holger Bührle construit Hulg, une goélette en aluminium de 22 mètres. Depuis 25 ans, cet autodidacte consacre sa vie à un projet hors norme, une œuvre qui mêle technicité et ingéniosité. Retour dans cette première partie sur un chantier unique en son genre où chaque étape incarne la persévérance et le rêve d'un tour du monde.
La naissance d'un rêve au long cours
Holger Bührle n'a rien d'un constructeur naval traditionnel. Électricien de formation, il s'est tourné vers la navigation par passion, bien qu'il habite à plus de 500 km de l'océan. Cette distance géographique ne l'a jamais freiné, bien au contraire. ''Si je devais attendre d'être au bord de la mer pour commencer, je n'aurais jamais rien fait'', confie-t-il.
Sa passion pour la mer remonte à son adolescence, bien avant son projet de construction. Né dans la région de Bade, il découvre la voile à 14 ans sur le lac Schluchsee où il obtient son permis A. Ce fut un coup de foudre immédiat. Par la suite, il multiplie les navigations en mer, notamment avec son oncle dans le sud de la France et en Grèce, ce qui renforce son désir de vivre de cette passion. Il commence par des dériveurs, puis s'aventure sur un Tornado, mais l'appel du grand large se fait pressant.
En 1998, il réalise sa première traversée de l'Atlantique à bord du Kritter, un deux-mâts de 25 mètres. Ce voyage marque un tournant dans son parcours et lui donne l'envie de concevoir un bateau capable de naviguer autour du monde tout en étant durable et adapté à un équipage réduit. C'est en découvrant les plans de l'Hydraduo, dessinés par l'architecte naval Kurt Reinke, qu'Holger Bührle pose les bases de son projet. Inspiré par ces lignes, il décide d'adapter le design à ses propres ambitions.
Le chantier commence modestement dans son jardin, loin de la mer, au milieu des collines boisées de la Forêt-Noire. Cet éloignement géographique, loin d'être un frein, devient le symbole d'un défi personnel pour Holger . ''Construire un bateau ici, c'est transformer un rêve lointain en réalité tangible, jour après jour'', avance-t-il.
Des erreurs pour se former
Autodidacte, il apprend les techniques de construction navale à force de recherches, d'expérimentations et d'erreurs qu'il considère comme une partie essentielle du processus. À chaque étape de construction, il s'impose ainsi des standards de qualité qu'il juge nécessaires pour les conditions extrêmes qu'il souhaite affronter en mer. Le choix de l'aluminium, matériau robuste et léger, s'impose rapidement pour sa résistance à la corrosion, essentielle lors de longues traversées en milieu isolé. ''Ce n'est pas qu'un bateau que je construis, c'est une vision de liberté et d'autosuffisance'', explique-t-il. Ce rêve se traduit par une quête de perfection qui le pousse à travailler jour après jour, parfois seul, parfois avec l'aide de passionnés venus lui prêter main-forte.
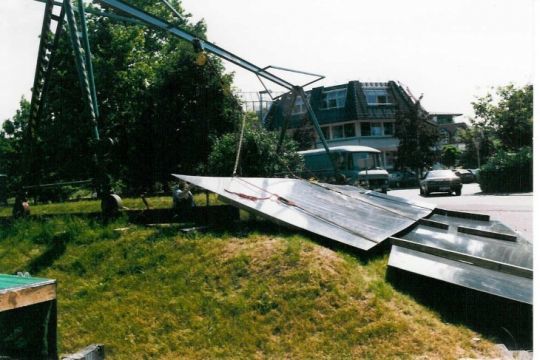
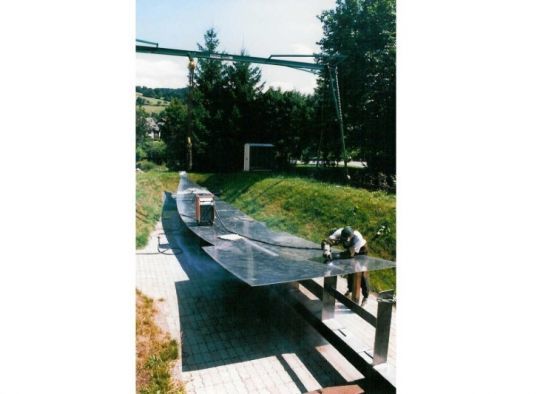
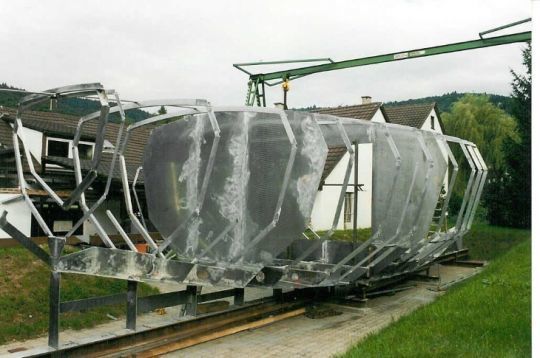
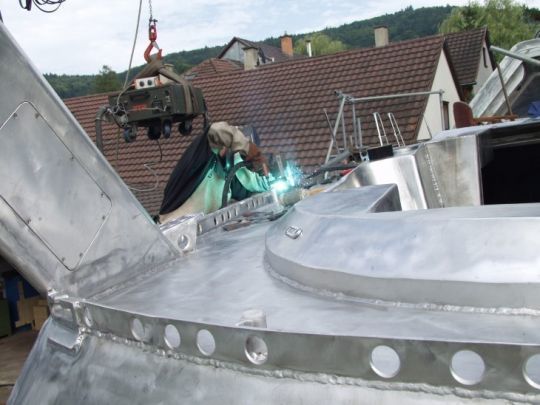
La coque : des procédés exigeants
La coque en aluminium est le cœur technique de Hulg. Avec son design à quille longue, elle offre au bateau une bonne stabilité tout en limitant son tirant d'eau à 2 mètres. Ce plan d'architecture assure un bon comportement sous voile et facilite les échouages si nécessaire.
L'utilisation de panneaux d'aluminium marins de haute qualité, découpés et soudés manuellement avec une précision chirurgicale, a permis de réduire le poids total du bateau tout en garantissant une étanchéité parfaite ainsi qu'une résistance structurelle optimale.
Les compartiments étanches intégrés à la coque, utilisés comme réservoirs d'eau et de carburant, ajoutent non seulement à la capacité de stockage mais contribuent également à équilibrer le bateau en navigation.
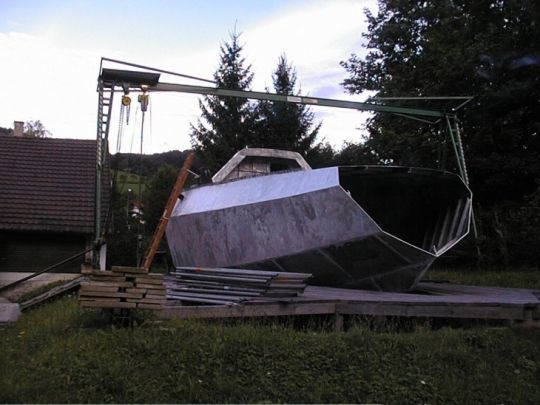
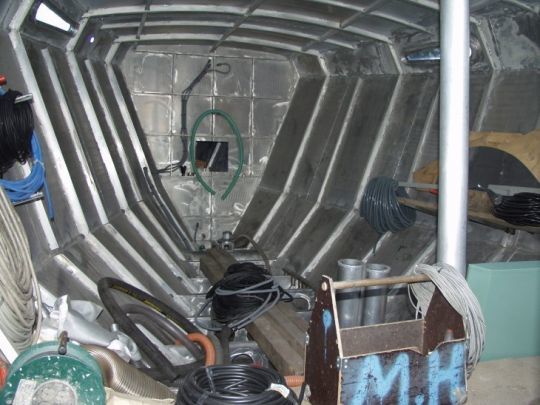
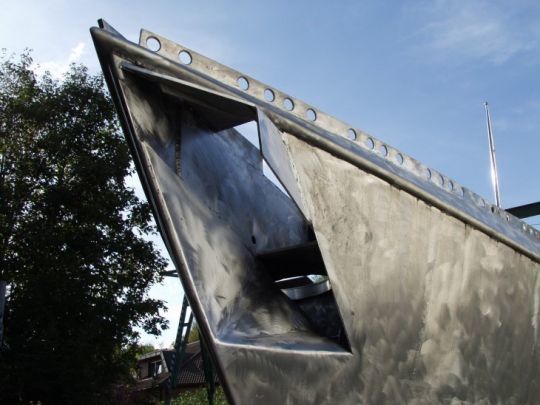
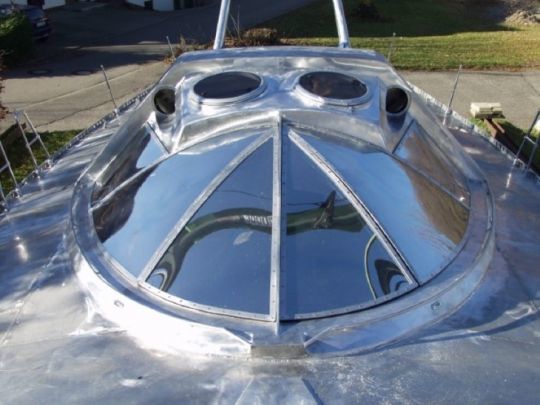
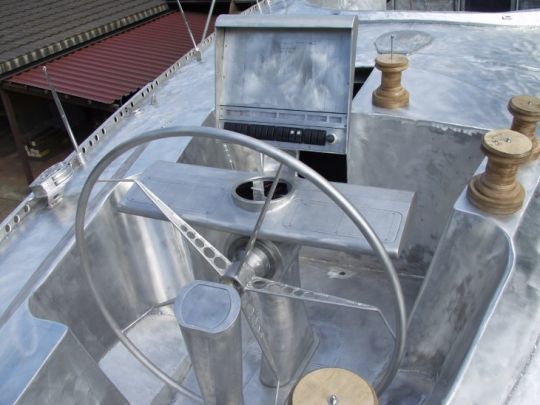
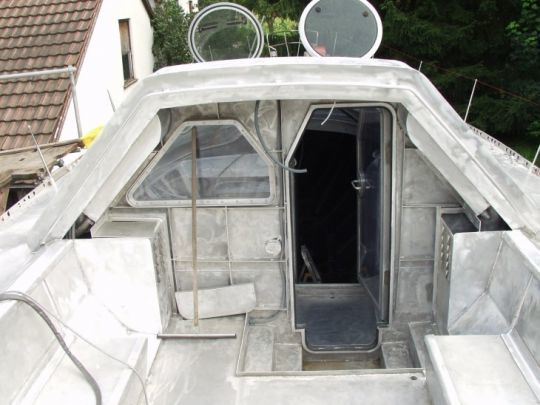
La fabrication de la quille : un procédé technique
Holger a opté pour une approche minutieuse et pragmatique dans la fabrication de la quille de son bateau. Le processus a débuté par la soudure du moule. La quille, qui n'était remplie qu'à moitié de plomb, nécessitait une plaque intermédiaire pour créer un réservoir dans la partie supérieure. Des trous de soudage auxiliaires ont été ajoutés pour permettre l'extraction du carburant et la soudure interne. La fermeture des plaques de 8 mm à l'avant a été un défi pour Holger nécessitant une gestion minutieuse de la chaleur pour éviter la déformation de la quille. Le bord supérieur a été laissé avec un surplomb de 10 cm pour des ajustements futurs. Une fois le moule en place, Holger a dû préparer l'espace sous le bateau pour installer la quille. Le terrain a été creusé et deux poutres en acier ont été utilisées comme rails pour glisser la quille sous le bateau. En raison de l'ajout de plomb à côté de la coque, il a fallu trouver une solution pour déplacer la quille de 3 mètres latéralement en utilisant une technique inspirée des méthodes égyptiennes avec des rouleaux ouverts.
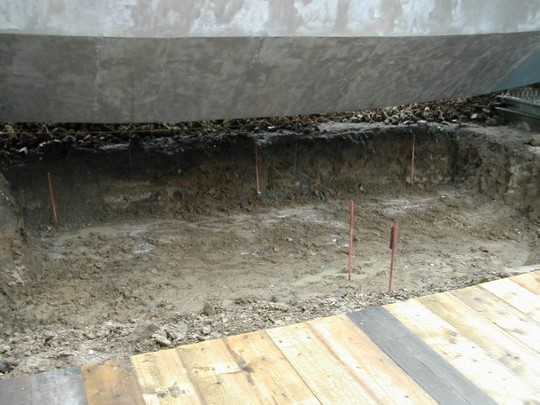
La coulée de plomb s'est étalée sur deux jours non-stop. Le travail a été exigeant, dégageant une fumée jaune enveloppant la zone d'habitation, tandis que l'équipe de Holger coulait du plomb par portions de 100 kg, couche par couche. Chaque couche de plomb devait refroidir sous l'eau ce qui a rendu l'opération particulièrement délicate. Après un temps de refroidissement et de régénération, la quille a été ajustée selon le gabarit. Le réglage final a eu lieu uniquement à la position finale où le fuselage reposait sur deux poutres en acier ajustables en hauteur à l'aide de tiges filetées. Cela a permis de compenser les mouvements de terrain. Enfin, une fois la quille en place, le bord a été chanfreiné, et quatre couches de soudure ont été appliquées pour finaliser la fabrication de cet élément crucial du bateau.
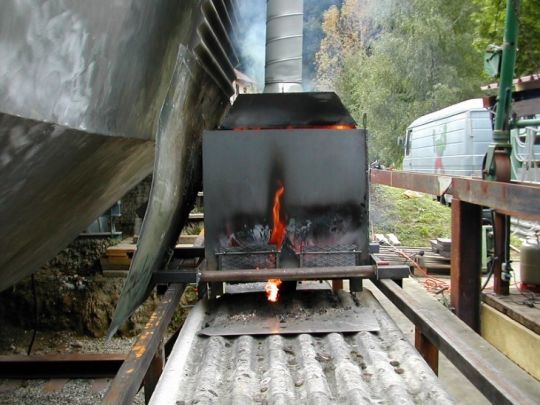
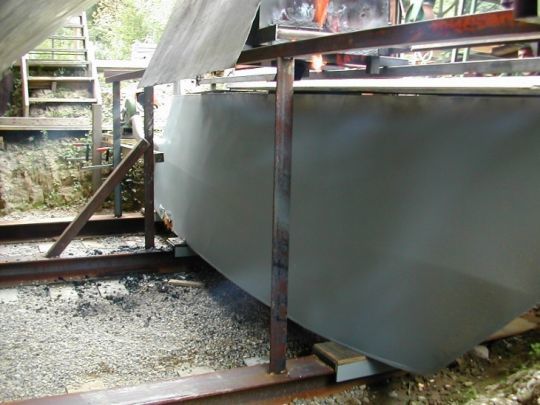
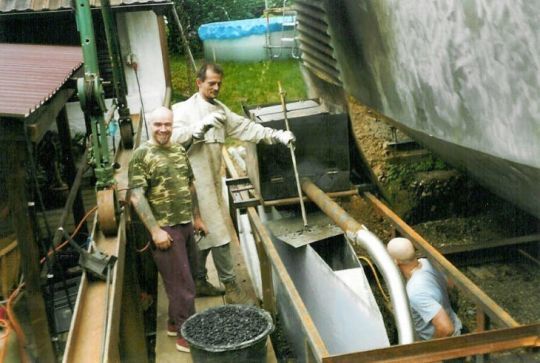
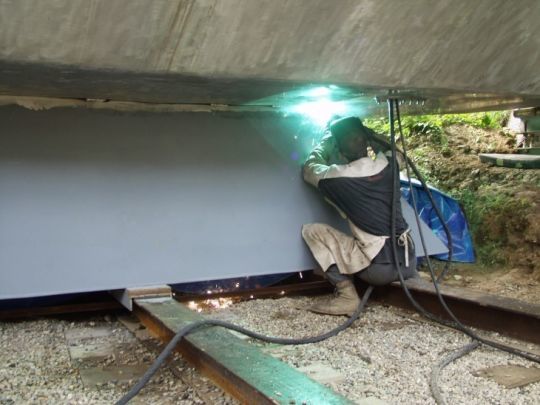
Un pont à l'épreuve du temps
Le pont, revêtu d'un teck de 8 mm, repose sur une plaque support de 6 mm pensée pour limiter les effets des variations de dilatation. Pour l'ensemble du jointoiement et du collage, Holger a privilégié des produits Sika, notamment le composé de nivellement particulièrement efficace pour corriger les irrégularités fréquemment observées sur une terrasse métallique. Son objectif était de conserver un pont le plus dégagé et fluide possible, une approche illustrée par l'intégration de grands taquets d'amarrage dépliables XXL, discrets une fois repliés.
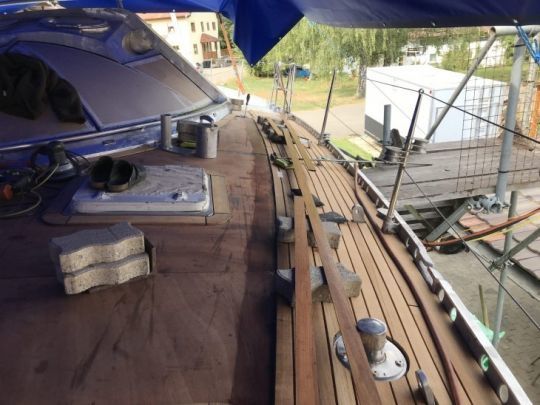
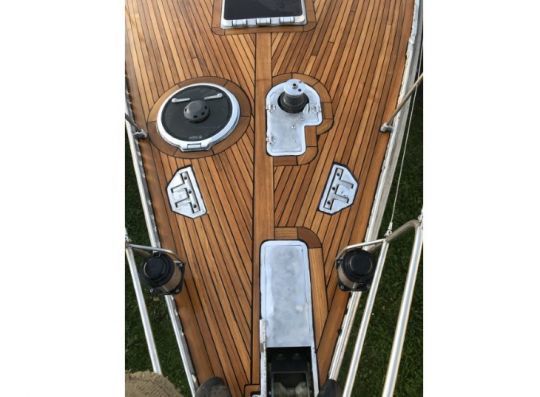
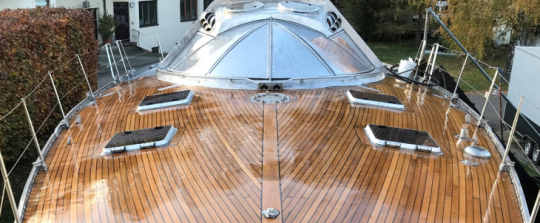
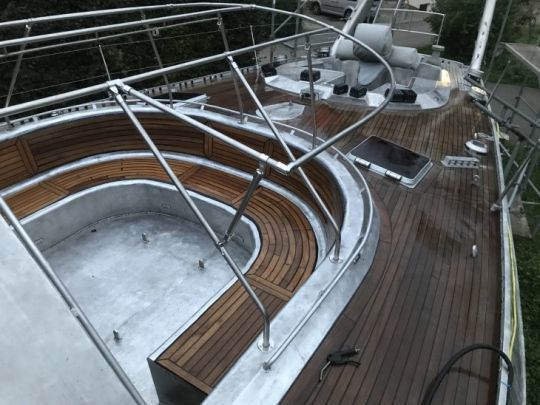
Un gréement conçu pour la performance et la durabilité
Dotée d'un mât principal de 22,5 mètres et d'un mât d'artimon de 19,5 mètres, le voilier bénéficiera d'une grande surface vélique. Des voiles modernes, entièrement lattées, seront montées sur des systèmes de chariots à rouleaux qui faciliteront leur manipulation. Les winches, les enrouleurs de foc et les systèmes de tension seront actionnés hydrauliquement, une prouesse technique qui apporte confort et précision dans toutes les conditions.
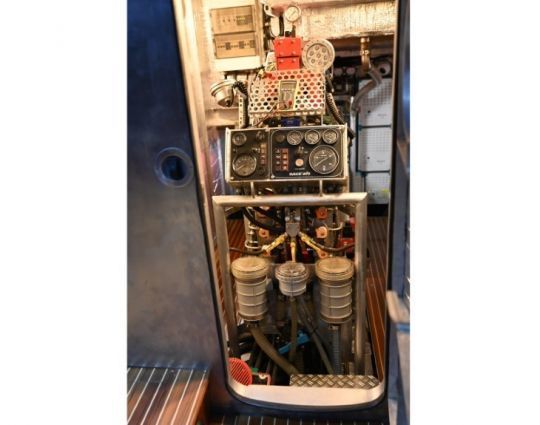