Coque rigide ou semi-rigides, tout est possible
En 2009, Patrick Bardon lançait la marque Sealver avec le Waveboat 525, une coque rigide de 5,25 m capable d'embarquer 6 personnes dont la particularité est d'être propulsé par un jet-ski. Un concept qui permet d'associer sports nautiques et plaisance, le tout dans une seule embarcation.
Sealver développe donc une gamme de 3 coques rigides de 4,44 m à 6,56 m et 2 semi-rigides de 5,75 m et 6,26 m. Pour chacun de ses bateaux, le chantier développe un kit de comptabilité pour les trois grandes marques de jet-ski, à savoir Yamaha, Seadoo et Kawasaki, avec une propulsion de 90 à 300 CV.
La marque s'est toujours adaptée aux tendances jets du moment, en permettant aux pilotes de pouvoir changer à tout moment pour la dernière nouveauté jet, tout en gardant la compatibilité avec leur Wave Boat.
Ainsi la marque propose aujourd'hui un kit adapté pour chaque coque soit 3 kits pour Yamaha, 2 pour Kawasaki et 3 pour Seadoo, inclut le kit pour la toute nouvelle coque ST3.

Allier sports nautiques et plaisance
La gamme Sealver s'adapte à un programme de navigation varié : balade en famille ou entre amis, vitesse (50 nœuds pour le WB 575), pêche ou encore sport de glisse tracté. Le chantier décline une version Wake de ces modèles avec un roll-bar.
Mais le gros avantage des Wave Boat reste leur propulsion par jet-ski. Arrivés au mouillage, on peut laisser une partie de la famille à bord et continuer d'aller naviguer et de s'amuser sur son jet.
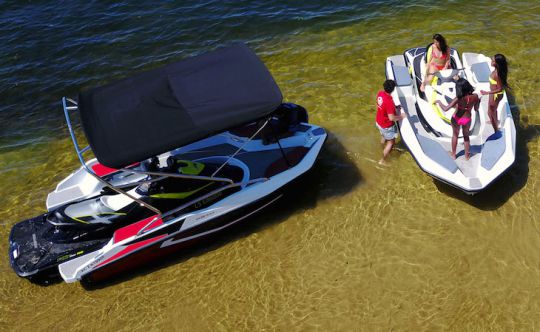
Une gamme qui s'adapte sans cesse au marché
Seadoo vient de lancer la nouvelle coque ST3 – plus design, plus large pour une meilleure stabilité avec un centre de gravité plus bas et une conception améliorée, cette coque s'adapte à merveille au large.
Toujours dans l'idée de suivre cette tendance jet qui évolue régulièrement, Sealver propose désormais un kit de compatibilité pour cette coque. Et dans une optique d'innovation, le chantier landais qui produit ses bateaux en interne dans son chantier naval de Sanguinet utilise la réalité virtuelle.
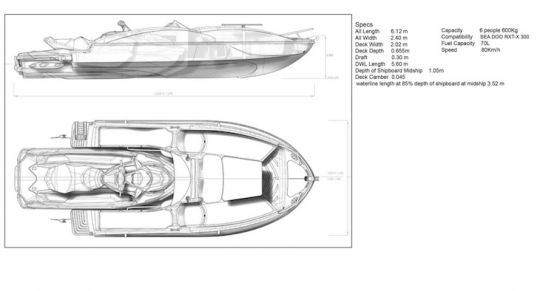
Un processus de digitalisation
Pour développer ce kit, le chantier landais s'est fait prêter une machine par Seadoo afin de commencer un processus de digitalisation de la coque et produire un kit de compatibilité pour ce jet. C'est-à-dire qu'une empreinte numérique du jet est réalisée (par la société CETIM sud-ouest) et les données envoyées à la société italienne XM TECH qui produit les moules des bateaux. Les pièces sont ensuite fabriquées au chantier par rotomoulage (mise en forme par moulage des matières plastiques).
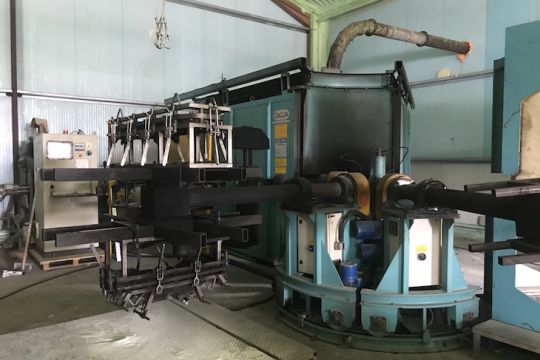
Grâce à la réalité virtuelle – que le chantier utilise depuis 2016 –, le chantier optimise sa conception et sa production. Contrairement à la 3D, la réalité virtuelle permet de se rendre immédiatement compte des volumes et évite l'utilisation des maquettes à l'échelle 1. Ainsi, le chantier peut produire ces kits de compatibilité pour le jet-ski soit parfaitement encastré dans le bateau.
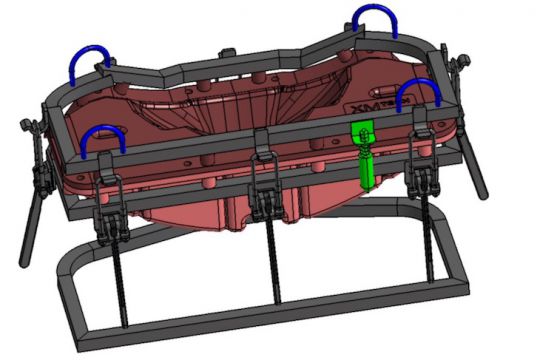
Aperçu numérique de la piece interface avant pour kit ST3 créé par XM tech sur la base de la numérisation faite par CETIM Sud-ouest.